VACUUM DEWATERED FLOORING:-
- Er S G Ashok Kumar PMP, IGBC-AP
- Jul 26, 2021
- 5 min read
· INTRODUCTION :-
The VDF was originally invented by Termix AB, Sweden many years ago. A flooring work for civil structures that is both time efficient and medium to high workability process to create a facility that is safe, healthy and comfortable concrete flooring to be done by used of vacuum dewatering concrete flooring (VDF) technology.
VDF Flooring in 5000 Sq ft, Rs 80 /square feet Grid Cubes Private Limited. This process is a means to efficiently remove excess water from newly placed, compacted and leveled concrete surfaces. Vacuum dewatering greatly improves the abrasion, largely exposed to hot weather conditions and impact resistance of the concrete surface.
It is preferably used in making concrete roads, railway platforms, industrial floors, bridges, RCC Roads, Pre-cast Concrete Products etc.
The vacuum dewatering results in coarse aggregate in the fresh mix being drawn to the top surface a further contributing factor in achieving wear-resistant concrete surfaces the surface of vacuum treated concrete is free of pitting, an important consideration for abrasion resistance and the possible exposure to a continuous flow of liquid over the member.
Technologies applied in concrete flooring will improve concrete flooring physical behavior. This method used like concrete flooring in warehouse, concrete road, parking area, production area in industrial buildings The vacuum dewatering is used widely throughout Europe today and in Sweden this method is used for 40 to 50 percent of all concrete floors.
· DEFINITION: -
The VDF flooring is termed as the kind of special type of flooring technique to achieve the high quality of concrete floors where the key is dewatering of concrete by vacuum process where in the surplus water from the concrete is removed immediately after placing and vibration, thereby reducing the water cement ratio to the optimum level is known as VDF flooring. It is also known as vacuum dewatered flooring.
With this technique, both these workability and high strength are possible at the same time. The system is workable for laying high quality concrete floors with superior cost effectiveness to achieve High strength, Durability, Longer Life, Better Finish and Faster Work.
· NEED OF VACCUM DEWATERED FLOORING :-
There are certain fundamental requirements due to which the vacuum dewatered flooring is preferred to be adopted in large scale flooring work in railway platforms, industrial floors, bridges, RCC Roads, Pre-cast Concrete Products.
The following are the basic needs of vaccum dewatered flooring are given below :-
1- The uncontrolled removal of water from the concrete matrix can result in adverse effects such as plastic shrinkage cracking.
2- Excessive bleeding of concrete can negatively interfere with surface characteristics such as resistance to wear.
3- The water added to a concrete mix generally exceeds the optimum required amount of water required to fully hydrate the cement constituent.
4- The additional water functions as a lubrication medium to allow mixing, placing and consolidation.
5- In hot and windy conditions, it produces concrete of high quality & durability.
· MATERIALS REQUIREMENT FOR VACUUM DEWATERED FLOORING: -
The following considerations in materials requirement are necessary prior to start of vacuum dewatering concrete flooring given below:-
Concrete Grade In vacuum dewatered flooring, the grade of concrete used shall be as –
a) M20-25 where Industrial Floors, Car Parking, Railway Platform, Workshop floors are planned to be laid.
b) M30-60 where Highways, Airport, RCC Roads are planned to be laid.
1- Cement
The cement selected should be appropriate for the intended use as provided for in the specifications. Vacuum treatment of concrete gives better results with Portland cement to increase the compressive strength of concrete.
2- Fine Aggregate –
Locally available sand is used as fine aggregate in the concrete mix. The test procedures as mentioned in IS-383 shall be followed to determine the physical properties of fine aggregate.
3- Coarse Aggregate
Crushed stone aggregates ranging from 10mm to 20mm sizes shall be used in respective proportions in concrete mixes. The aggregates shall be tested in accordance to IS-383.
4- Water – As per recommendation of IS: 456, the water to be used for mixing and curing of concrete should be free from deleterious materials. Therefore potable water shall be used in all operations demanding control over water quality.
· EQUIPMENTS USED IN VDF SYSTEM:-
The following are the equipments used in the VDF system are listed below:-
1- Double beam screed vibrator.
2- Vacuum pump with hose.
3- Suction mat.
4- Power float.
5- Power trowel.
1- Double beam screed vibrator:-
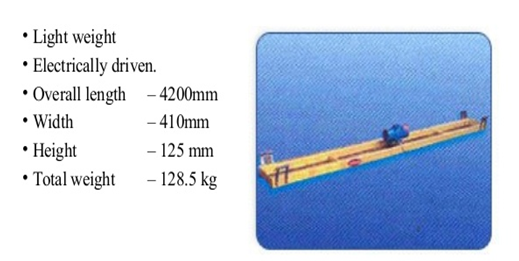
Fig -1 double beam screed vibrator
The double beam screed vibrator is used for levelling as well as compaction of concrete. Two passes are required to achieve maximum compaction. Self-contained water protective vibrator motor is mounted on the centre of the beam. It is also known as surface vibrator.
2- Vaccum pump with hose:-
This system consists of the magnitude of the applied vacuum pump is usually about 0.08MPa, which reduces water content about 15-20%. Vacuum Pump is mounted on transportation trolley and powered by Electric Motor of 5 to 10 HP.
The vacuum pump is connected through a Hose (pipe) with the mat to remove the surplus water from fresh concrete. The mat consists of two layers, one is in direct contact with green concrete to prevent removal of cement with water and other used for extraction of water through pipe.

Fig -2 vacuum pump with hose
3- Suction mat :-
The suction mat is an large single PVC sheet. The suction mat under the surface nylon cloth is placed to act as very fine filter. The top mat is provided with junction box and short hose. The size of the mat may be ranges 7.5*5.0m or as the panel size.

Fig -3 suction mats
4- Power float:-
The power float is an surface grinding equipment. It grinds the surface to make it wear resistance. The over all height of this float is 980 mm , floating speed is 120 RPM and its weight is 140kg.

Fig -4 power float
5- Power trowel :-
The power trowel is an surface finishing equipment. Its polishes the surface after floating operations. The over all height of the power trowel is 980mm, trowelling speed is 120RPM and its equipment weight is 145kg.

Fig -5 polishing the surface by using power trowel
· MERITS OF VDF FLOORING :-
The following are the merits of the vacuum dewatered flooring are listed below: -
ü Compressive strength is increased.
ü W/C proportion is reduced, which prompts early setting and high quality.
ü Cement consumption is reduced as no cement is required separately for finishing.
ü Abrasion resistance is increased.
ü Wear resistance is increased.
ü There are minimum dusting & crack formation.
ü There are minimum dry and plastic shrinkage and floor wraps.
ü There is uniform homogeneous floor with high flatness accuracy.
ü There is lower water permeability due to increased density.
ü High early strength minimizes damage on newly cast floors.
ü Maintenance cost is reduced.
· DEMERITS OF VDF FLOORING:-
The following are the demerits of VDF flooring are listed below:-
Ø High initial cost or starting expense.
Ø Need prepared work for the vacuum dewatering process.
Ø Need specific equipment or explicit hardware for vacuum dewatering like vacuum siphon.
Ø Need power utilization during dewatering process.
Ø Need trained labour.
· APPLICATIONS OF VDF FLOORING :-
The following are the applications of VDF flooring are listed below:-
1- Ware houses.
2- Godowns.
3- Roads , sport courts
4- Cellars , parking areas
5- Production areas
6- Pharmaceutical companies and
7- Base floor for epoxy and PU floorings.
· REFERENCES:-
1- Guidelines on WSC Agenda Item No. 004/01/05 issued by Works Directorate/RDSO on “Standardization of specification of flooring, Roofing Material for Platform covering in Station Premises & Standardization of Specification of Workshop Flooring”
2. IS 2571 (1970): Code of practice for laying in-situ cement concrete flooring
3. “Specifications for Civil Works 2015”, Department of Construction, Services and Estate Management, Department of Atomic Energy, Govt. of India.
4- Vacuum Dewatered Cement Concrete Roads – A Review (Source: https://www.ijert.org/research/vacuum-dewatered-cement-concrete-roads-areview-IJERTCONV8IS11046.pdf)
BLOG AUTHOR DETAILS:-
BABA AFRID .S
CMTI Campus Ambassador
4th YEAR , Mother Theresa institute of engineering and technology -MTIET
PALAMNER -CHITTOR DISTRICT
Comments